To the exciting future
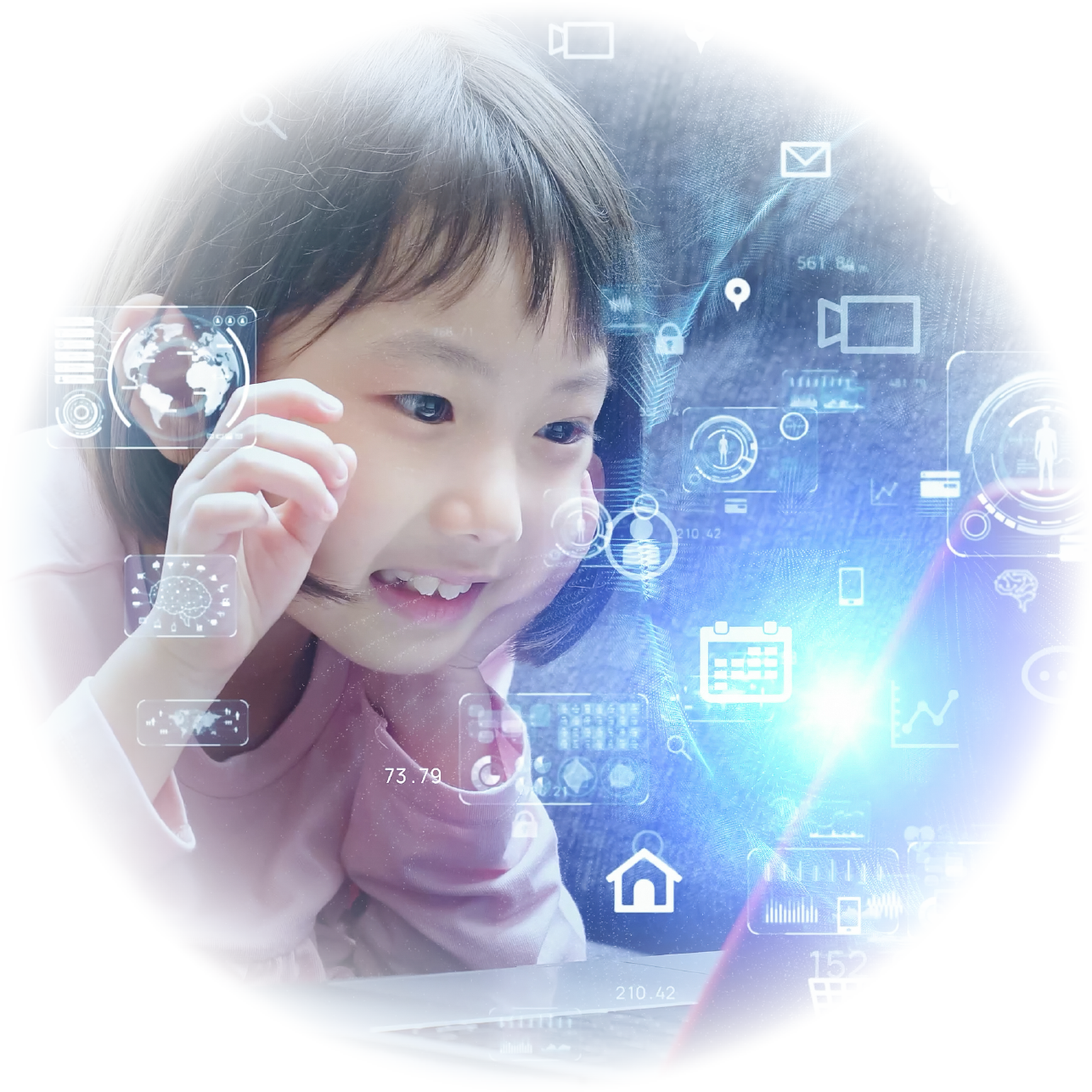
We believe that technology originally exists to make the world, society, and people happy.
Whether it's the great invention of the century or the small technological innovation that never catches the eye, it always leads to the world's happy progress somewhere. That's why we work diligently on our daily work.
What kind of happiness will this technology create in the future?
What kind of technology will we need for future happiness?
Converting such imagination into infinite energy, we will steadily update society and ourselves with ideas, technology, and execution. We are Sumitomo Heavy Industries Mechatronics Division.
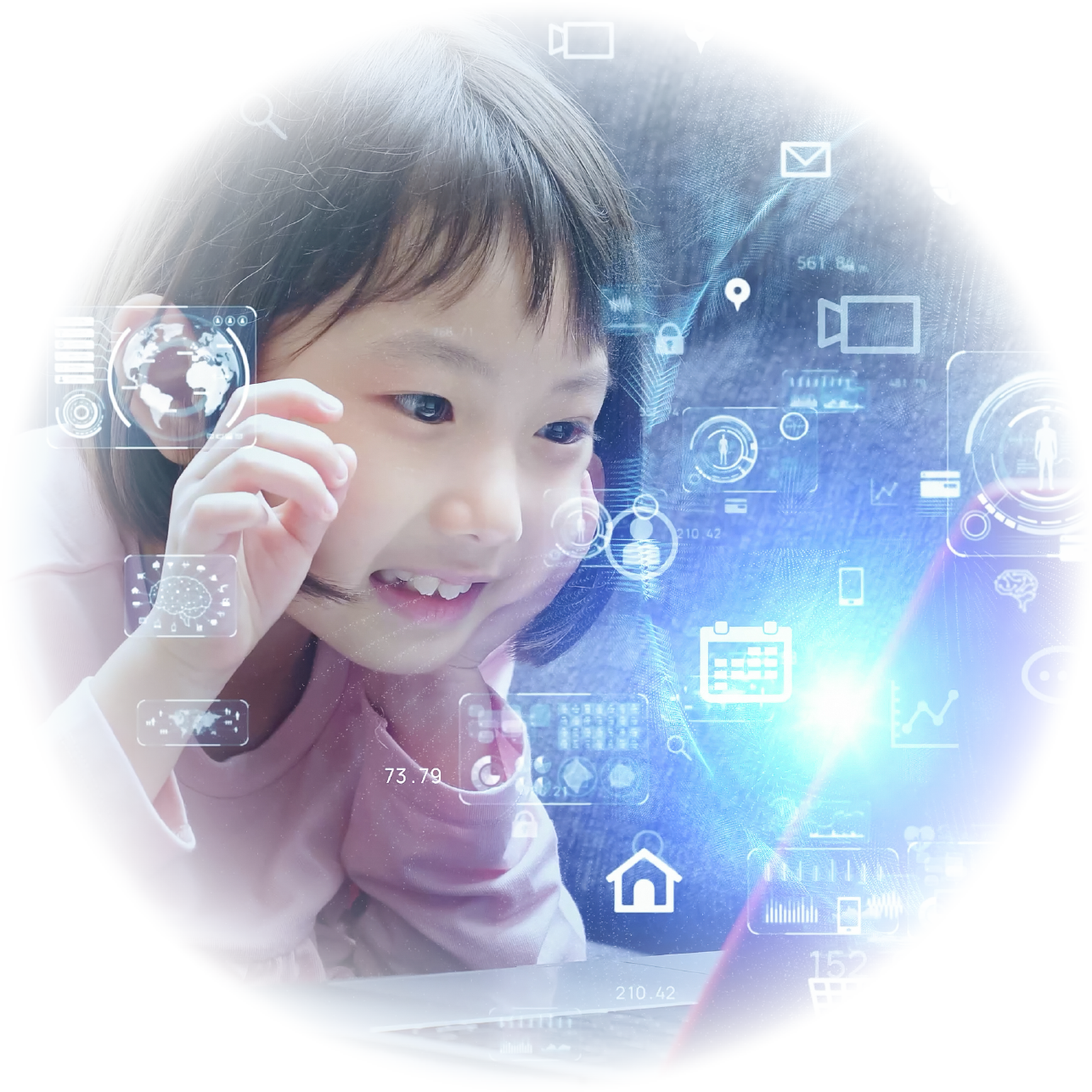
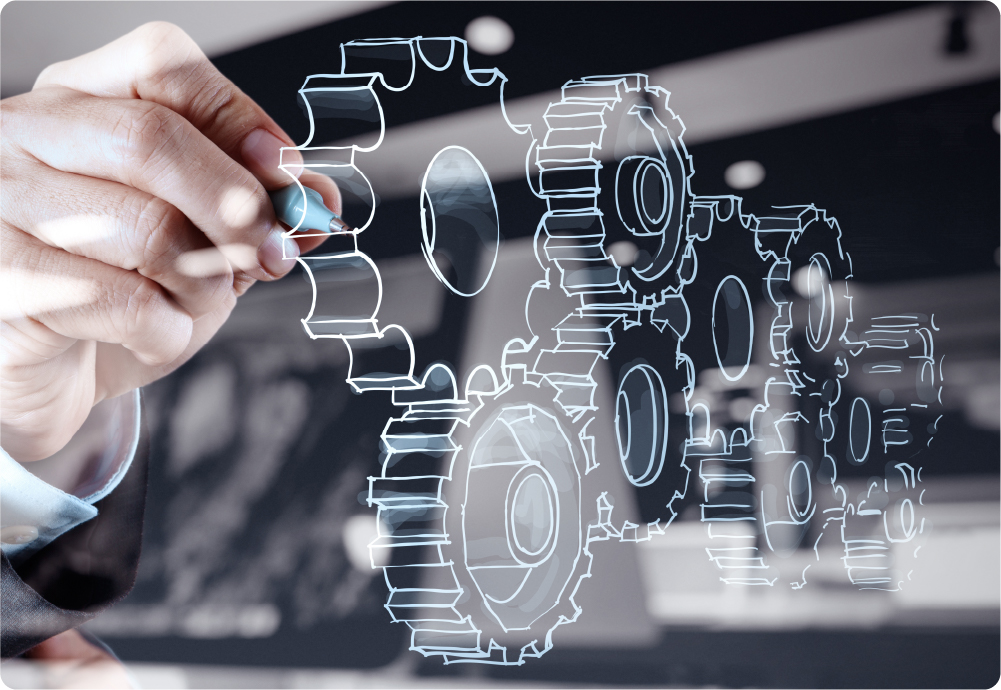
Business
From components to total systems, we will combine our accumulated experience to create even higher product value.
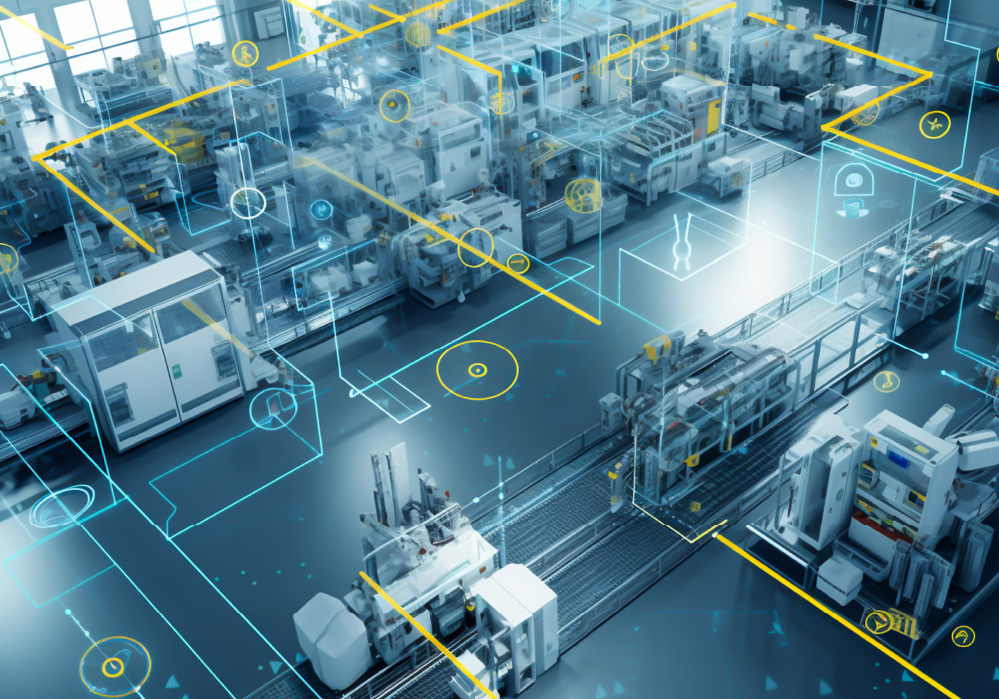
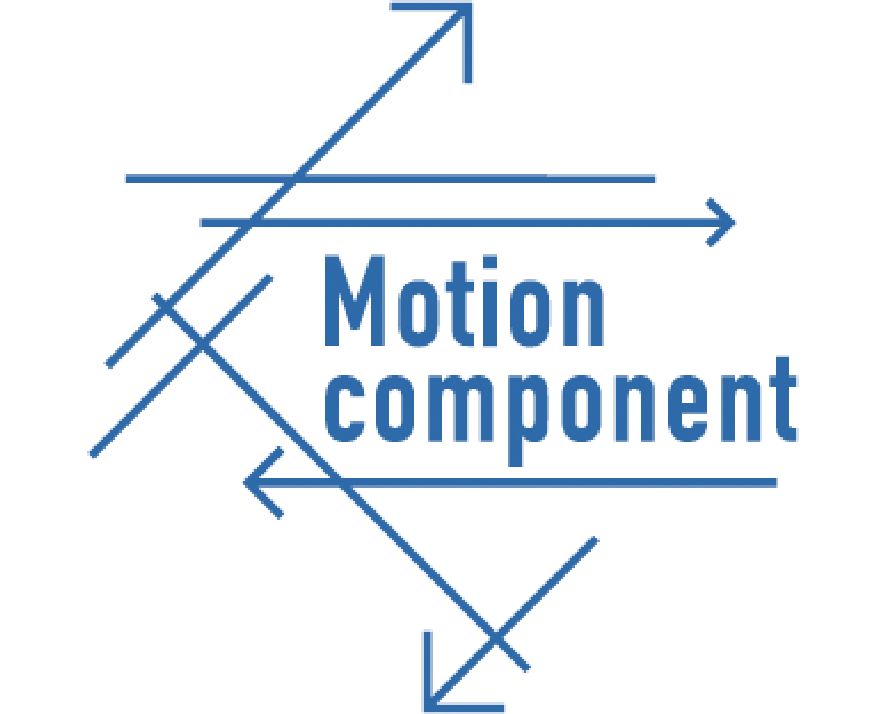
Motion Component
Make equipment movement more accurate and precise.
We will improve the accuracy and precision of the movements of the machines that support the world, and make the infrastructure of future society run smoothly.
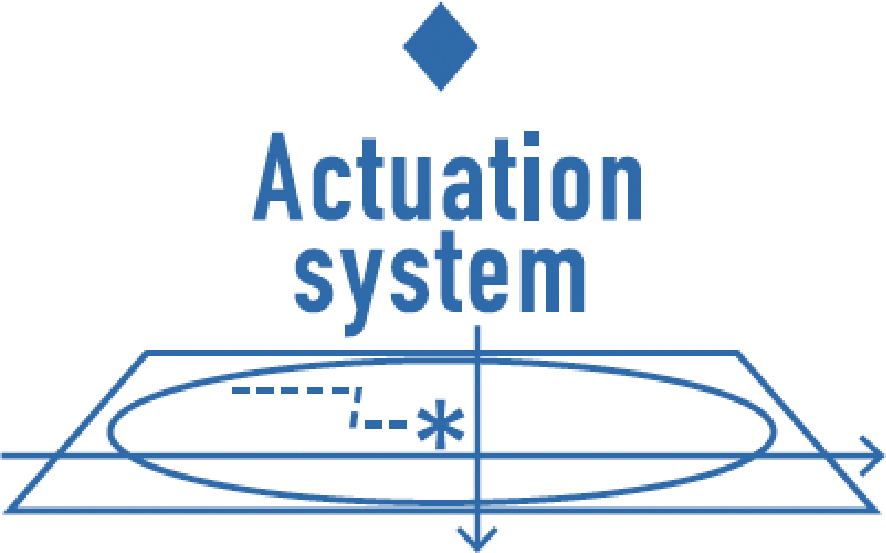
Actuation System
Continuing to update the world with nano-level technology.
A drive mechanism that controls ultra-fine movements at the nano level.
We realize all kinds of future possibilities, such as power savings and increased data communication capacity.
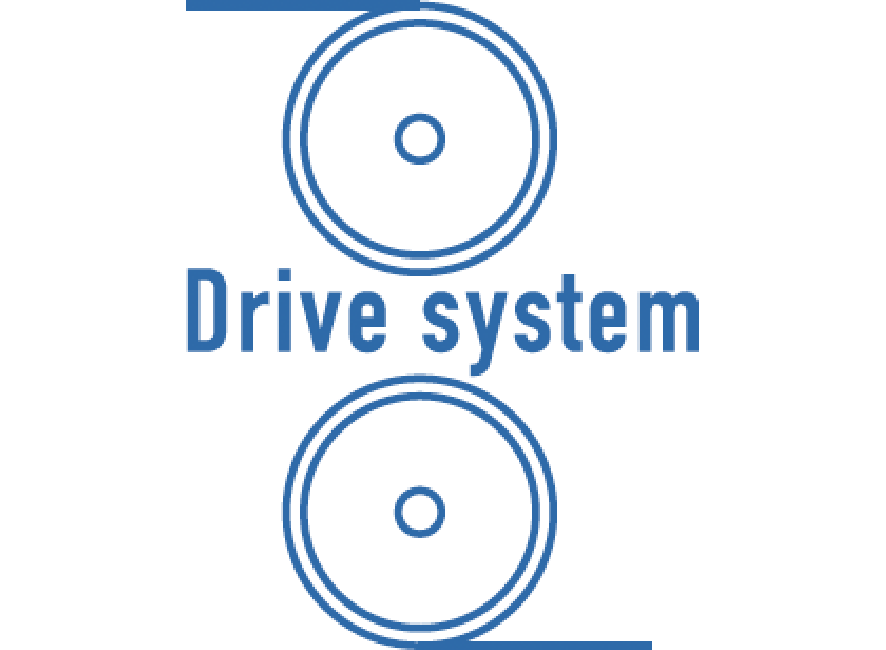
Drive System
Harmonize complex motor movements.
A control system ideal for Roll-to-Roll equipment that freely controls multiple motors.
We make manufacturing more precise and contribute to the mass production of next-generation products.
We will realize an eco-friendly and carbon-neutral world.
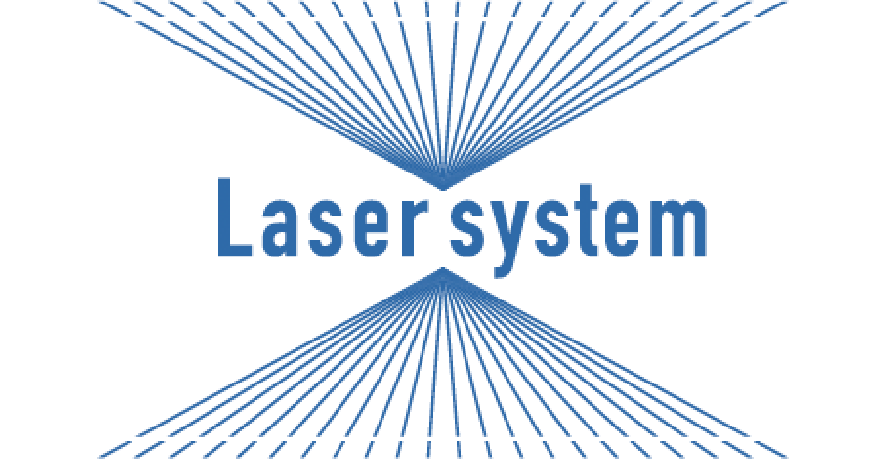
Laser System
Opening up the future with lasers and illuminating the world.
We will contribute to the miniaturization, higher functionality, and cost reduction of a wide variety of future devices, and support a sustainable society by improving the performance of parts.
News release
-
Contributing to a decarbonized society with laser annealing system for SiC power device that is essential for EV
- Laser Annealing
- Solution
2025.02.19
-
Laser Annealing - Power Semiconductor Manufacturing
- Laser Annealing
- Tech Information
2024.07.29
-
Worldwide after-sales service Locations
- Laser Annealing
- Solution
2024.01.29
-
Selecting the laser source for SiC laser annealing equipment, an essential technology for manufacturing power semiconductors
- Laser Annealing
- Solution
2021.12.01
-
Offering real-time water surface monitoring and stable quality control for wafer surface during the manufacturing of power semiconductors
- Laser Annealing
- Solution
2021.12.01